产品检索
产品类别
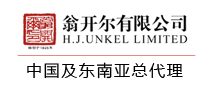
2012-7-6 10:59:18
因为润滑条件和作用是有限的,在许多情况下,金属零件摩擦面之间会出现互相接触,另外,因工作条件不同,有时不宜采用润滑剂等。所以研究金属材料表面磨损是相当有必要的。前面已说过,影响金属材料耐磨性的因素多且复杂,这里仅简述金属材料力学性能与显微组织这两个影响因素,巨着重于磨料磨损方面。
金属材料的硬度与其它力学性能(强度、塑性等)存在一定的关系,用硬度方法来研究材料耐磨性较为一方便,在硬度与耐磨性关系方面的报道也较多,故这里主要简述硬度这一影响因素。
一般认为,金属材料耐磨性可由表面硬度来衡量,因材料表面硬度反映材料表面抵抗过载的能力。此外,材料硬度又可近似确定表层材料的强度。这一理论对于粘着磨损较为适应。枯着磨损时,在没有其它条件影响的情况下,金属材料的磨损率随着材料硬度升高而降低。脆性材料比塑性材料具有较高抗粘着能力。塑性材料的粘着破坏,常发生在离表面的一定深度处,磨削下来的颗粒较粗大。脆性材料的磨损产物呈金属磨屑状,破坏深度较浅。同膝多数命属材料,当外界应力大于材料硬度的三分之一时,便发生由轻微磨损向严重磨损的转变可见,提高材料表面硬度可降低磨损量,尤其是当外界压应力较大时,更应如此。另外,相同金属或相同晶格类型、晶格间距、电子密度和电化学性能相近的金属,它们彼此间的互溶性大,容易粘着,耐擦伤性差,摩擦副选材时应特别注意这一特点。
真实剪断抗力代表实际晶体在外力作用下,沿某一滑移面,从抵抗滑移开始直至剪切断裂为止的全部过程的抗力。实际磨损过程中的微观切削(塑性犁沟等),都是剪切断裂过程,此真实剪断抗力与耐磨性关系更为密切。表示钢的耐哦性与真实剪断抗力的关系。
对于扩展性表面疲劳磨损,当金属零件承受较大的交变载荷材料塑性较差,在磨损过程的跑合阶段就会出现小麻点,经一定时间后小麻点便发展成痘斑状剥落坑,即出现二次和三次剥落,最后导致零件的失效。例如轴承零件的显微组织中,控制适当的残余奥氏体量,可提高零件塑性,从而延长零件使用寿命。表示轴承件疲劳寿命与残余奥氏体量的关系。再如锻模的模腔经表面强化处理后可明显提高耐磨性,但表面强化又引起表面韧性的下降,在冲击负荷作用下,于模腔的转角处易出现磨裂现象。
最新产品